半干法是把脫硫全過程和脫硫物質(zhì)解決各自選用不一樣的情況反映,特別是在濕情況下脫硫、在干情況下解決脫硫物質(zhì)的半干法,不僅有濕式脫硫工藝反應(yīng)靈敏、脫硫效率高的優(yōu)勢,又有干法脫硫工藝無污水廢水排出、在干情況下解決脫硫物質(zhì)的優(yōu)點,是除硫工藝關(guān)鍵發(fā)展前景。
The semi dry process reflects the different selection of the whole desulfurization process and desulfurization materials, especially the semi dry process of desulfurization in wet conditions and solving desulfurization materials in dry conditions. It not only has the advantages of sensitive response and high desulfurization efficiency of wet desulfurization process, but also has the advantages of dry desulfurization process without sewage and wastewater discharge and solving desulfurization materials in dry conditions. It is the key development prospect of sulfur removal process.
1、噴霧器半干法
1. Spray semi dry method
工藝詳細介紹
Detailed introduction of process
噴霧器半干法是運用噴霧干燥機基本原理,將吸附劑漿體做霧化噴到脫硫塔。在脫硫塔內(nèi),吸附劑在與煙塵中的二氧化硫發(fā)上化學(xué)變化的另外,消化吸收煙塵中的發(fā)熱量使吸附劑中的水份揮發(fā)干躁,脫硫反映后的廢料以干態(tài)排出來。
The spray semi dry method uses the basic principle of the spray dryer to spray the adsorbent slurry to the desulfurization tower. In the desulfurization tower, the adsorbent changes chemically with the sulfur dioxide in the flue dust. In addition, the heat in the flue dust is digested and absorbed to make the water in the adsorbent evaporate and dry, and the waste after desulfurization is discharged in a dry state.
優(yōu)點和缺點
merits and demerits
工藝步驟比白云石-熟石膏法簡易,項目投資也較小。缺陷是脫硫率較低,一般為70-80%、實際操作延展性較小、鈣硫比較高,運作成本增加、副產(chǎn)品沒法運用。
The process steps are simpler than dolomite gypsum method, and the project investment is also small. The defect is that the desulfurization rate is low, generally 70-80%, the actual operation ductility is small, the calcium sulfur is relatively high, the operation cost increases, and the by-products cannot be used.
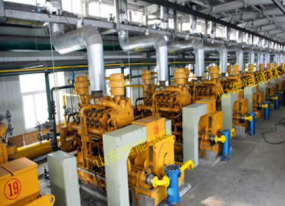
2、爐內(nèi)噴鈣尾端加濕活*法
2. Calcium Spraying in furnace, tail end humidification method
工藝詳細介紹
Detailed introduction of process
將研磨石灰石粉用氣力輸送系統(tǒng)方式 噴涌到爐內(nèi)上端溫度為900~1250℃的地區(qū),CaCO3馬上溶解并與煙塵中的SO2和小量的SO3反映轉(zhuǎn)化成CaSO4。在內(nèi)爐內(nèi)中未反映的CaO與噴到的水反映轉(zhuǎn)化成Ca(OH)2,SO2與轉(zhuǎn)化成Ca(OH)2快速響應(yīng)轉(zhuǎn)化成CaSO3,有一部分被氧化成CaSO4。
The ground limestone powder is sprayed into the area with the temperature of 900 ~ 1250 ℃ at the upper end of the furnace by means of pneumatic conveying system. CaCO3 is dissolved immediately and reflected with SO2 and a small amount of SO3 in the smoke and dust and transformed into CaSO4. Cao not reflected in the inner furnace is converted into Ca (OH) 2 by reaction with the injected water, SO2 is converted into Ca (OH) 2 by rapid response and converted into CaSO3, and some of it is oxidized into CaSO4.
優(yōu)點和缺點
merits and demerits
優(yōu)勢是機器設(shè)備項目投資較小,可是在提升爐內(nèi)噴鈣標(biāo)準(zhǔn)下,CaCO3熱裂解轉(zhuǎn)化成基酶CaO,盡管無法立即在爐膛內(nèi)獲得很高的脫硫率,但爐內(nèi)未與SO2反映的CaO在加熱爐后側(cè)灑水加濕、水合為Ca(OH)2,超低溫下可再度與SO2反映,能明顯提升系統(tǒng)軟件脫硫率和鈣基吸著劑使用率,但脫硫率較一般在60%~70%??偟膩砜?爐內(nèi)脫硫率和鈣基吸著劑使用率都不足高,其技術(shù)經(jīng)濟發(fā)展特性的競爭能力不足強。
The advantage is that the investment of machinery and equipment projects is small. However, under the standard of calcium injection in the furnace, CaCO3 is thermally cracked and converted into basic enzyme Cao. Although it is impossible to obtain a high desulfurization rate in the furnace immediately, Cao not reflected with SO2 in the furnace is watered and hydrated to Ca (OH) 2 at the back of the heating furnace. It can be reflected with SO2 again at ultra-low temperature, which can significantly improve the desulfurization rate of system software and the utilization rate of calcium based sorbent, but the desulfurization rate is generally 60% ~ 70%. On the whole, the desulfurization rate in the furnace and the utilization rate of calcium based sorbent are not high enough, and the competitiveness of its technical and economic development characteristics is not strong enough.