垃圾填埋場中收集到的填埋氣,經(jīng)填埋氣預(yù)處理系統(tǒng)將填埋氣中的H2S、H2O等除去,再經(jīng)過填埋氣壓縮機加壓至0.5MPa·G,然后再通過催化脫氧將填埋氣中的O2脫除,然后再經(jīng)過變壓吸附工藝將填埋氣提純至車用壓縮天然氣,后經(jīng)過加臭、CNG壓縮機加壓至20MPa·G直接經(jīng)加氣柱充入CNG運輸管束車。
The landfill gas collected in the landfill site will be removed from the H2S and H2O in the landfill gas by the landfill gas pretreatment system, and then pressurized to 0.5MPa · G by the landfill gas compressor. Then, the O2 in the landfill gas will be removed by catalytic deoxidation. Then, the landfill gas will be purified to vehicle compressed natural gas by the pressure swing adsorption process, and then pressurized to 20MPa · G by the odorization and CNG compressor, and directly charged into the CNG transport tube bundle through the gas column.
3.1 預(yù)處理系統(tǒng)
3.1 Pretreatment system
預(yù)處理系統(tǒng)是垃圾填埋場填埋氣利用工程中的一個重要環(huán)節(jié),該系統(tǒng)不僅用于實現(xiàn)對填埋氣的增壓、穩(wěn)壓、溫度調(diào)節(jié)、除雜質(zhì)、脫水、脫硫、除臭和安全保護等處理功能,同時還是垃圾填埋場氣體收集系統(tǒng)與提純系統(tǒng)之間的燃氣輸送橋梁。
The pre-treatment system is an important link in the utilization engineering of landfill gas in landfills. It is not only used to achieve the functions of pressurization, pressure stabilization, temperature regulation, impurity removal, dehydration, desulfurization, deodorization, and safety protection of landfill gas, but also serves as a gas transmission bridge between the landfill gas collection system and the purification system.
垃圾填埋氣(LFG)由羅茨風機抽采進入預(yù)處理系統(tǒng)。預(yù)處理系統(tǒng)設(shè)置降溫除水除塵裝置。系統(tǒng)入口設(shè)置初級過濾器以過濾LFG中的大顆粒雜志及部分液態(tài)水;設(shè)置一臺換熱器將原料氣溫度降至20℃以內(nèi),使原氣體中的飽和水份以游離態(tài)析出,后經(jīng)氣液分離器有效去除,分離器除水率達97%以上;風機后端設(shè)置一水冷換熱器用于調(diào)節(jié)預(yù)處理系統(tǒng)出口溫度;預(yù)處理系統(tǒng)出口設(shè)置精密過濾器,以保證氣體中固體雜志有效去除。脫硫采用干式脫硫工藝,脫硫劑采用固體氧化鐵,同時為了提高脫硫劑的利用效率,本工程粗脫硫部分設(shè)計兩臺脫硫塔,兩塔之間可以并聯(lián)也可以串聯(lián)操作。除臭系統(tǒng)采用雙塔吸附,一塔再生的工藝,以保證系統(tǒng)能夠連續(xù)運行。
Landfill gas (LFG) is extracted by Roots blower and enters the pre-treatment system. The pre-treatment system is equipped with a cooling, water removal, and dust removal device. The system inlet is equipped with a primary filter to filter large particulate matter and some liquid water in LFG; Set up a heat exchanger to reduce the temperature of the raw material to within 20 ℃, allowing the saturated water in the original gas to precipitate in a free state. After that, it is effectively removed by a gas-liquid separator, with a water removal rate of over 97% in the separator; A water-cooled heat exchanger is installed at the rear end of the fan to regulate the outlet temperature of the pre-treatment system; A precision filter is installed at the outlet of the pre-treatment system to ensure the effective removal of solid magazine in the gas. The desulfurization adopts a dry desulfurization process, and the desulfurization agent uses solid iron oxide. In order to improve the utilization efficiency of the desulfurization agent, two desulfurization towers are designed for the coarse desulfurization part of this project, which can be operated in parallel or in series. The deodorization system adopts a dual tower adsorption and one tower regeneration process to ensure continuous operation of the system.
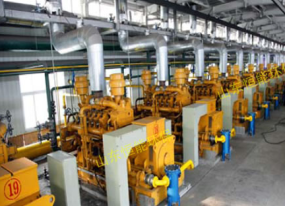
3.2螺桿壓縮
3.2 Screw compression
為了實現(xiàn)變壓吸附提純裝置的佳分離效果,原料氣必須被壓縮到適合PSA工作的工藝壓力。壓縮機采用整體橇裝式噴油螺桿壓縮機,工藝氣壓力和流量穩(wěn)定,同時出口氣路設(shè)置冷卻設(shè)備以調(diào)節(jié)氣體溫度。原料氣壓縮機采用噴油螺桿壓縮機,設(shè)計出口壓力0.6MPa,排氣量2250Nm3/h,出口溫度40℃。
In order to achieve optimal separation efficiency of the pressure swing adsorption purification device, the feed gas must be compressed to a process pressure suitable for PSA operation. The compressor adopts an integral skid mounted oil injection screw compressor, with stable process gas pressure and flow rate. At the same time, cooling equipment is installed in the outlet gas circuit to regulate gas temperature. The raw material gas compressor adopts an oil injection screw compressor, with a designed outlet pressure of 0.6MPa, a displacement of 2250Nm3/h, and an outlet temperature of 40 ℃.
3.3催化脫氧系統(tǒng)
3.3 Catalytic deoxygenation system
催化脫氧是在催化劑的作用下使填埋氣中的O2和CH4、H2或者甲醇(乙醇)等氣體反應(yīng)脫除。本工程原料氣為垃圾填埋氣,在催化脫氧過程中不需要引入外源物質(zhì),直接利用氣體中的甲烷進行催化燃燒,減少配套工程。
Catalytic deoxidation is the reaction between O2 and gases such as CH4, H2, or methanol (ethanol) in landfill gas under the action of a catalyst. The raw gas for this project is landfill gas. During the catalytic deoxidation process, no external substances need to be introduced, and methane in the gas is directly used for catalytic combustion, reducing the need for supporting projects.
具體脫氧工藝為:原料氣經(jīng)壓縮、出脫硫塔后進入脫氧前余熱回收系統(tǒng),可實現(xiàn)原料氣預(yù)熱以達到精脫硫工作溫度及脫氧催化劑起活溫度,同時降低脫氧后氣體溫度,有效利用反應(yīng)熱源,降低裝置能耗,同時增加裝置安全性;脫氧催化劑采用設(shè)備廠家自主研發(fā)的低溫高效金屬催化劑,催化劑起活溫度在300℃以內(nèi),同時根據(jù)反應(yīng)溫度配比進氣量,維持催化燃燒反應(yīng)在較低溫度內(nèi),既能保證O2有效燃燒脫除,又能保證裝置在安全穩(wěn)定工況下運行;終經(jīng)余熱回收系統(tǒng)后氣體溫度仍較高,根據(jù)項目氣候溫度情況,采用風冷水及水冷雙重方式保證氣體溫度,既能為氣體降溫,又能有效利用自然環(huán)境降低裝置能耗。
The specific deoxidation process is as follows: the raw gas is compressed and discharged from the desulfurization tower before entering the pre deoxidation waste heat recovery system, which can achieve preheating of the raw gas to reach the working temperature of fine desulfurization and the activation temperature of the deoxidation catalyst. At the same time, the temperature of the deoxidation gas is reduced, the reaction heat source is effectively utilized, the energy consumption of the installation is reduced, and the safety of the device is increased; The deoxygenation catalyst adopts a low-temperature and high-efficiency metal catalyst independently developed by the equipment manufacturer, with the catalyst activation temperature within 300 ℃. At the same time, according to the reaction temperature ratio of the intake air, the catalytic combustion reaction is maintained at a lower temperature, which can not only ensure the effective combustion and removal of O2, but also ensure the installation operates under safe and stable working conditions; After passing through the waste heat recovery system, the gas temperature is still relatively high. Based on the climate and temperature situation of the project, a dual method of wind, cold water, and water cooling is adopted to ensure the gas temperature, which can not only cool the gas but also effectively utilize the natural environment to reduce energy consumption of the device.
3.4變壓吸附提純系統(tǒng)
3.4 Pressure swing adsorption purification system
變壓吸附法(PSA)是在加壓條件下,使CO2吸附在活性炭、分子篩、硅膠等吸附劑表明,以實現(xiàn)氣體分離脫除CO2。其工藝原理是利用吸附劑對不同組分氣體吸附力的不同,選擇性吸附混合氣體中的某些組分,使之與其他氣體組分得以分離。
Pressure swing adsorption (PSA) is a method of adsorbing CO2 onto adsorbents such as activated carbon, molecular sieve, and silica gel under pressurized conditions to achieve gas separation and removal of CO2. The process principle is to selectively adsorb certain components of the mixed gas by utilizing the different adsorption forces of adsorbents on different gas components, so as to separate them from other gas components.
本研究設(shè)計六個吸附塔,內(nèi)裝專用吸附劑,可有效保證產(chǎn)氣中甲烷純度在90%以上,甲烷回收率大于92%。裝置經(jīng)過吸附、均壓降壓、順放、均壓升壓、產(chǎn)品氣升壓過程后,吸附塔便完成了一個完整的“吸附—再生”循環(huán),又為下一次吸附做好了準備。
This study designs six adsorption towers with dedicated adsorbents inside, which can effectively ensure that the methane purity in the gas production is above 90% and the methane recovery rate is greater than 92%. After the device undergoes the processes of adsorption, equalizing pressure reduction, clockwise release, equalizing pressure increase, and product gas increase, the adsorption tower completes a complete "adsorption regeneration" cycle, and is ready for the next adsorption.
3.5CNG壓縮
3.5CNG compression
CNG壓縮機組采用一體化集成式壓縮機橇采用高效節(jié)能型壓縮機組,四缸五級壓縮,水平往復活塞式結(jié)構(gòu),機組整體橇裝,水冷自動帶隔音房型機組,機組采用高壓填料密封、無油潤滑結(jié)構(gòu)設(shè)計和無平衡段設(shè)計,強制少油潤滑運行。機組為四曲拐兩兩互成90°,使得機組平衡性較好。同時橇內(nèi)還配置進氣緩沖罐、回收裝置(集油罐)、儲氣瓶組和充氣柱(預(yù)留)。
The CNG compressor unit adopts an integrated compressor sled, which is an efficient and energy-saving compressor unit with four cylinders and five stages of compression, and a horizontal reciprocating plug structure. The unit is installed as a whole on a sled, with a water-cooled automatic soundproof room type unit. The unit adopts a high-pressure packing seal, oil-free lubrication structure design, and a balanced section design, and is forced to operate with less oil lubrication. The unit has four cranks arranged in pairs at a 90 ° angle to ensure good balance. At the same time, the sled is also equipped with an intake buffer tank, a recovery device (oil collection tank), an air storage bottle group, and an inflation column (reserved).
四、實際應(yīng)用
4、 Practical application
豐臺循環(huán)經(jīng)濟產(chǎn)業(yè)園垃圾填埋場項目每小時可產(chǎn)生填埋氣約為4000Nm3,原采用9個火炬進行燃燒的方式來處理填埋場產(chǎn)生的填埋氣。這樣的處理方式不僅沒有真正達到減少環(huán)境污染的目的,還造成嚴重的資源浪費。填埋氣燃燒時會排放出粉塵、二氧化硫、氮氧化物等有害氣體,這些氣體溶于水會形成酸雨和霧霾,對當?shù)丨h(huán)境造成污染。
The Fengtai Circular Economy Industrial Park Garbage Landfill Project can generate approximately 4000Nm3 of landfill gas per hour. Originally, 9 torches were used for combustion to treat the landfill gas generated by the landfill. This treatment method not only fails to truly achieve the goal of reducing environmental pollution, but also causes serious resource waste. When landfill gas is burned, harmful gases such as dust, sulfur dioxide, and nitrogen oxides are emitted. These gases dissolve in water and form acid rain and haze, causing pollution to the local environment.
為了達到資源的綜合利用,北京華泰潤達節(jié)能科技有限公司將豐臺區(qū)循環(huán)經(jīng)濟產(chǎn)業(yè)園垃圾填埋氣進行提純制車用天然氣,將收集來的垃圾填埋氣經(jīng)預(yù)處理(脫硫、脫水、除塵)系統(tǒng)、螺桿壓縮、催化脫氧系統(tǒng)、PSA系統(tǒng)及CNG壓縮系統(tǒng)等進行處理。該項目每年處理垃圾填埋氣為3504萬m3,可產(chǎn)生生物天然氣1900萬m3,每年可節(jié)約21024噸標煤,每年可減少CO2排放量約為70萬噸。將垃圾填埋氣提純制取天然氣,這樣不僅能減少有害氣體排放,還可以將廢氣資源化,產(chǎn)生更大的經(jīng)濟效益。
In order to achieve comprehensive utilization of resources, Beijing Huatai Runda Energy Conservation Technology Co., Ltd. will purify the landfill gas from the Fengtai District Circular Economy Industrial Park to produce natural gas for vehicles. The collected landfill gas will be processed through pre-treatment (desulfurization, dehydration, dust removal) systems, screw compression, catalytic deoxygenation systems, PSA systems, and CNG compression systems. This project processes 35.04 million cubic meters of landfill gas annually and can generate 19 million cubic meters of biological natural gas. It can save 21024 tons of standard coal per year and reduce CO2 emissions by approximately 700000 tons per year. Purifying landfill gas to produce natural gas can not only reduce harmful gas emissions, but also resource waste gas and generate greater economic benefits.